Machining Project
Fabricated a scaled train model using various machining techniques, from CAD design to metalworking, employing a range of machines to create precise components
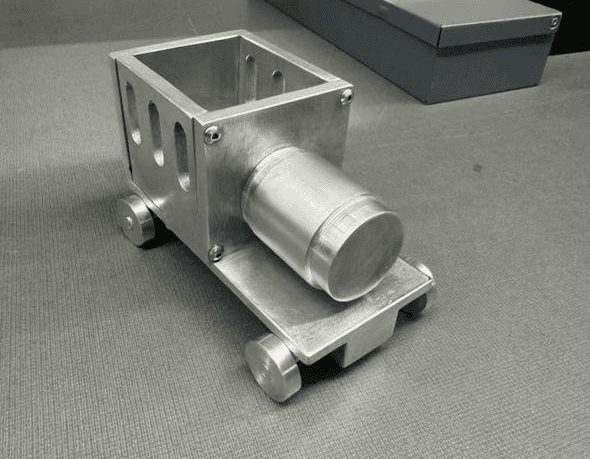
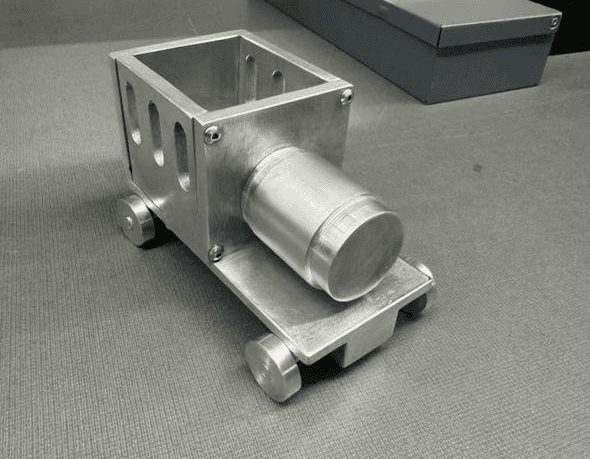
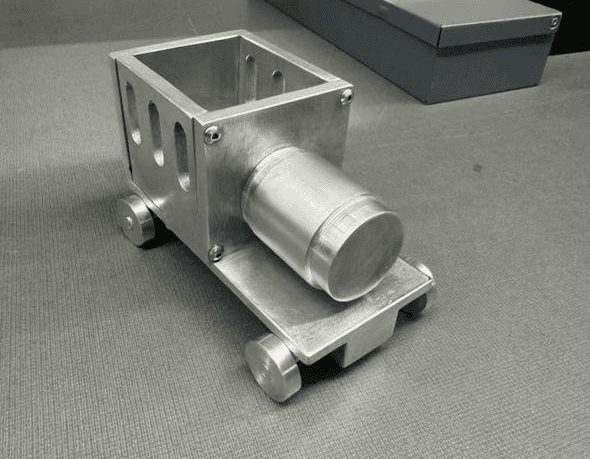
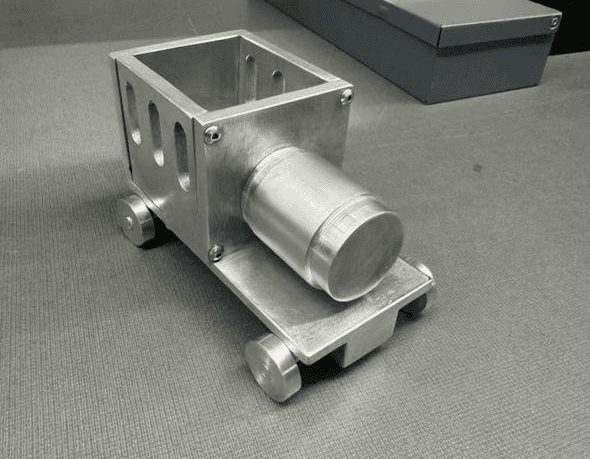
Industry
Industry
Manufacturing
Manufacturing
Hours
Hours
12
12
Skills
Skills
CAD, Milling, Lathing
CAD, Milling, Lathing
CAD, Milling, Lathing
Challenge
The goal of this project was to design and fabricate a scaled train model, focusing on the front section, including the cylindrical body and detailed wheels. Starting with a CAD model, I mapped out each component’s specifications, choosing suitable machining techniques to bring the design to life. One of the main challenges was ensuring dimensional accuracy and consistency across parts, especially for components like the cylinder, which needed to fit precisely with other sections, and the wheels, which required exact turning on the lathe to achieve smooth rotation and alignment.
Throughout the process, I utilized multiple machines to shape the metal parts. The cylindrical front section was fabricated using a combination of water jetting for rough shaping and milling for finishing details. The wheels were carefully turned on a lathe to achieve the required diameter and profile. Additional elements were crafted with CNC milling for intricate detailing, and I used various other metalworking tools to assemble and refine each component. This multi-step process required meticulous planning and precise execution to ensure each part fit seamlessly into the overall design.
Results
The final train model is a highly detailed and precise replica of the front section, showcasing the intricate craftsmanship possible through careful machining. I was particularly impressed with the level of detail achievable through the combination of water jetting, milling, and lathe work, as each process contributed a unique level of precision to different components. The wheels, in particular, demonstrated excellent rotational balance and alignment, which exceeded my initial expectations.
This project provided hands-on experience with various machining techniques, enhancing my skills in precision manufacturing and CAD-to-physical model translation. The process reinforced the importance of machine selection and setup in achieving accurate, high-quality results and demonstrated the collaborative potential of multiple machining processes to bring complex designs to life.
Challenge
The goal of this project was to design and fabricate a scaled train model, focusing on the front section, including the cylindrical body and detailed wheels. Starting with a CAD model, I mapped out each component’s specifications, choosing suitable machining techniques to bring the design to life. One of the main challenges was ensuring dimensional accuracy and consistency across parts, especially for components like the cylinder, which needed to fit precisely with other sections, and the wheels, which required exact turning on the lathe to achieve smooth rotation and alignment.
Throughout the process, I utilized multiple machines to shape the metal parts. The cylindrical front section was fabricated using a combination of water jetting for rough shaping and milling for finishing details. The wheels were carefully turned on a lathe to achieve the required diameter and profile. Additional elements were crafted with CNC milling for intricate detailing, and I used various other metalworking tools to assemble and refine each component. This multi-step process required meticulous planning and precise execution to ensure each part fit seamlessly into the overall design.
Results
The final train model is a highly detailed and precise replica of the front section, showcasing the intricate craftsmanship possible through careful machining. I was particularly impressed with the level of detail achievable through the combination of water jetting, milling, and lathe work, as each process contributed a unique level of precision to different components. The wheels, in particular, demonstrated excellent rotational balance and alignment, which exceeded my initial expectations.
This project provided hands-on experience with various machining techniques, enhancing my skills in precision manufacturing and CAD-to-physical model translation. The process reinforced the importance of machine selection and setup in achieving accurate, high-quality results and demonstrated the collaborative potential of multiple machining processes to bring complex designs to life.










