Six-DOF robotic arm using Arduino
I developed a 6-DOF robotic arm with custom CAD designs and 3D-printed parts, incorporating servo control and real-time manipulation using potentiometers.
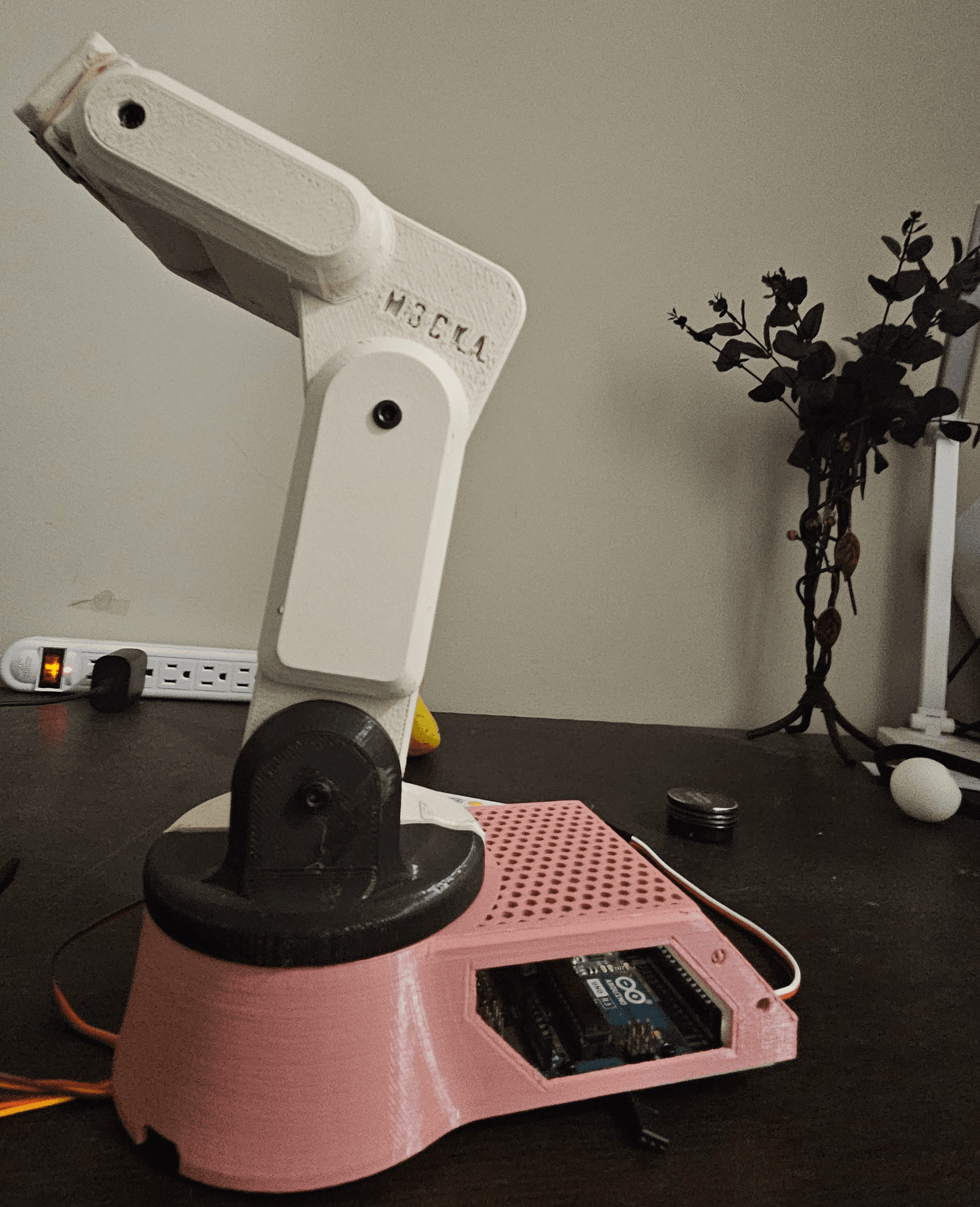
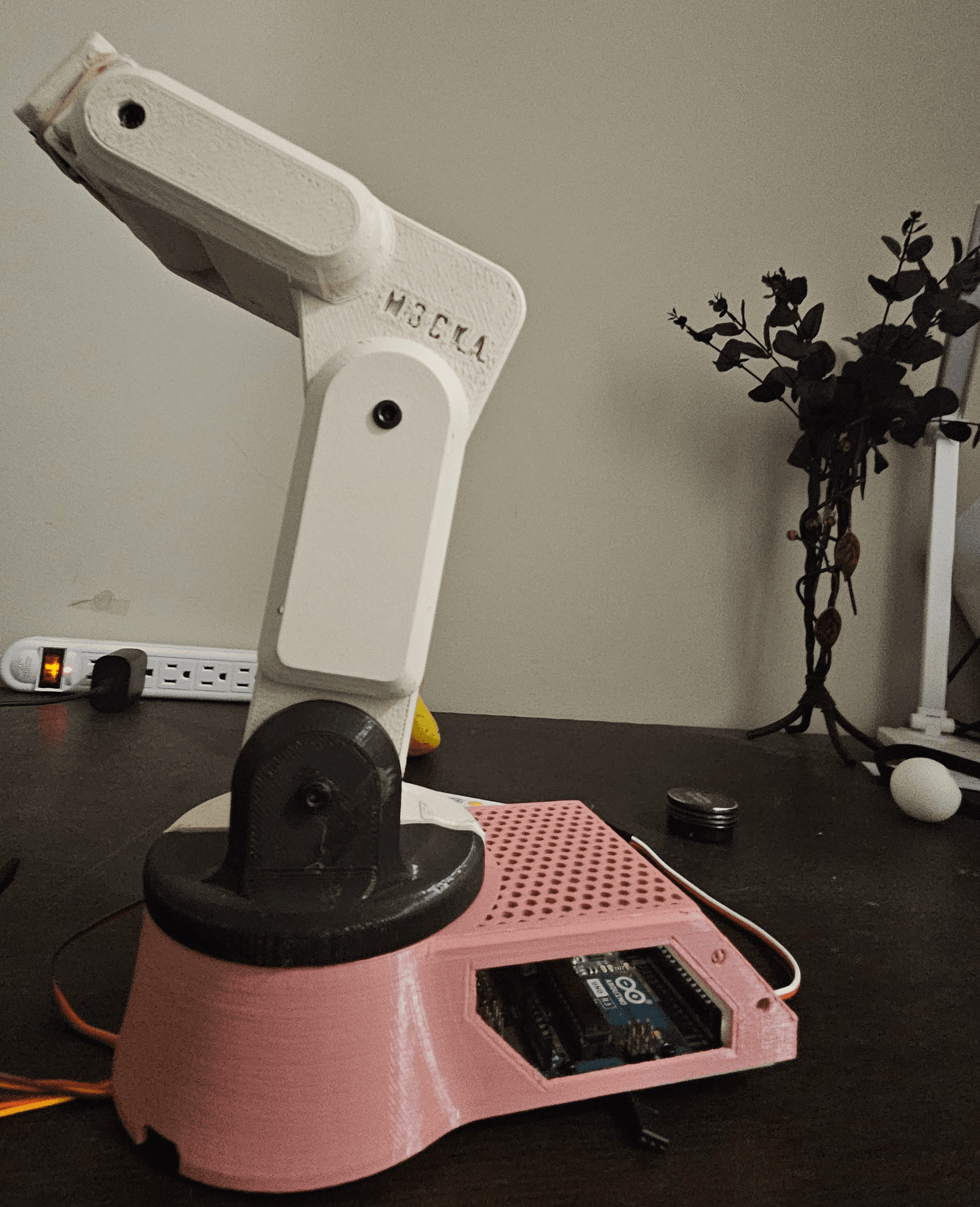
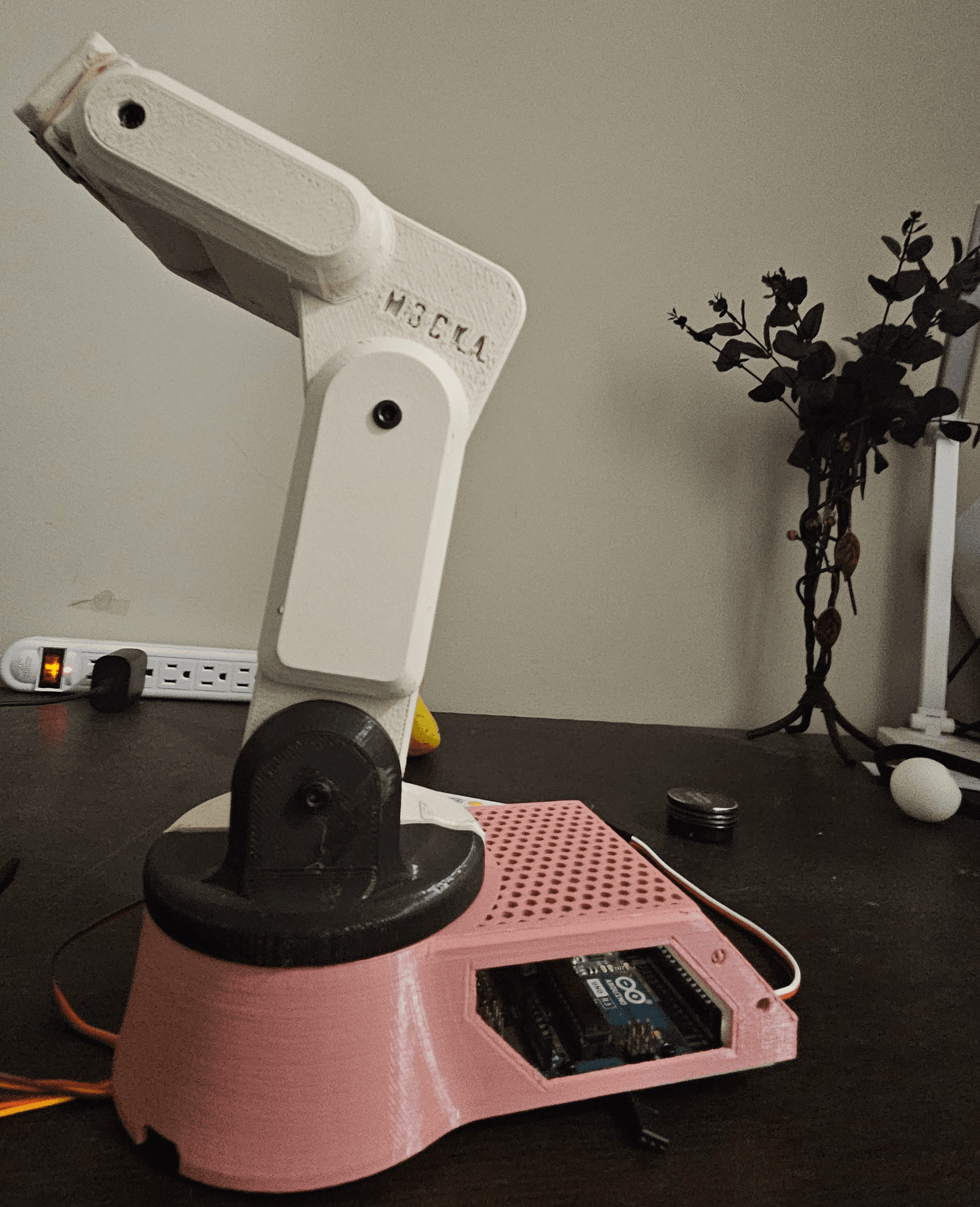
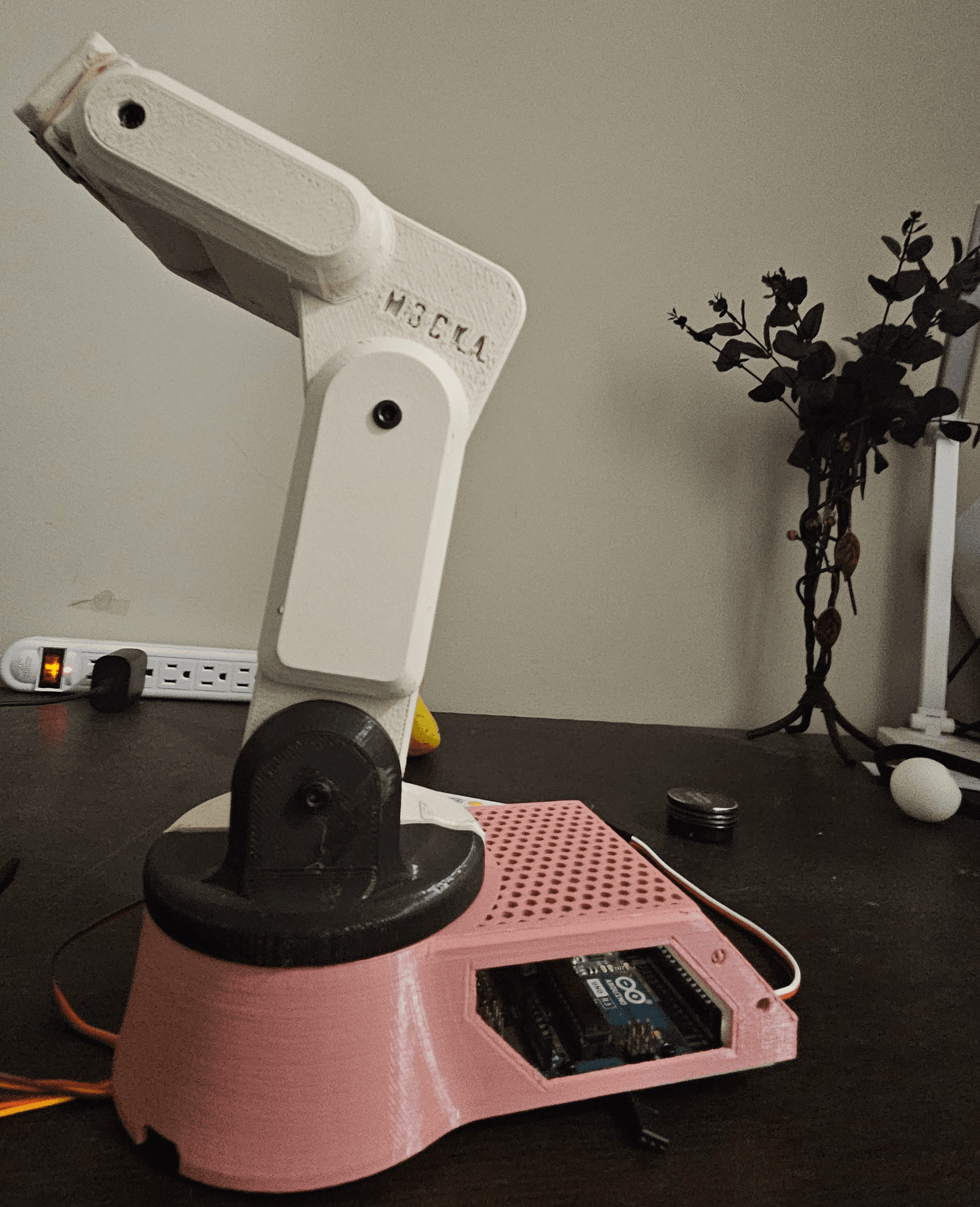
Industry
Industry
Robotics
Robotics
Hours
Hours
36
36
Skills
Skills
C++, CAD, Electronics
C++, CAD, Electronics
C++, CAD, Electronics
Challenge
The aim of this project was to design and build a fully functional 6-DOF robotic arm from scratch, with each joint powered by servo motors and controlled by an Arduino microcontroller. During the ideation phase, I explored different configurations to balance range of motion with stability, focusing on joint placement and material strength to ensure durability and flexibility.
The process involved iterating through CAD designs to ensure each joint could move freely while supporting the weight and stress of the arm in various positions. One of the primary challenges was programming synchronized motion across all servos to achieve smooth, coordinated movements essential for complex tasks. Additionally, creating a smaller version of the arm with potentiometers as analog controllers added another layer of complexity. This setup required precise calibration to translate small adjustments on the scaled-down model into accurate, real-time movements on the main arm, demanding a deep understanding of feedback control and Arduino programming.
Results
The completed 6-DOF robotic arm demonstrates high precision and responsiveness, capable of executing complex maneuvers with smooth, real-time control. I was particularly surprised by how effectively the potentiometer-based control on the smaller arm translated into intuitive manipulation of the main arm, allowing fine-tuned adjustments in each joint with minimal latency. The analog control enabled a hands-on feel for manipulating the robotic arm, which I didn’t anticipate would be so responsive in a real-world setup.
Additionally, the project highlighted the importance of joint alignment and load distribution, as minor adjustments in the CAD design greatly influenced the arm's stability and fluidity. This experience deepened my understanding of mechanical and electrical integration, showcasing the potential of combining custom design, Arduino programming, and real-time control systems in robotics
Challenge
The aim of this project was to design and build a fully functional 6-DOF robotic arm from scratch, with each joint powered by servo motors and controlled by an Arduino microcontroller. During the ideation phase, I explored different configurations to balance range of motion with stability, focusing on joint placement and material strength to ensure durability and flexibility.
The process involved iterating through CAD designs to ensure each joint could move freely while supporting the weight and stress of the arm in various positions. One of the primary challenges was programming synchronized motion across all servos to achieve smooth, coordinated movements essential for complex tasks. Additionally, creating a smaller version of the arm with potentiometers as analog controllers added another layer of complexity. This setup required precise calibration to translate small adjustments on the scaled-down model into accurate, real-time movements on the main arm, demanding a deep understanding of feedback control and Arduino programming.
Results
The completed 6-DOF robotic arm demonstrates high precision and responsiveness, capable of executing complex maneuvers with smooth, real-time control. I was particularly surprised by how effectively the potentiometer-based control on the smaller arm translated into intuitive manipulation of the main arm, allowing fine-tuned adjustments in each joint with minimal latency. The analog control enabled a hands-on feel for manipulating the robotic arm, which I didn’t anticipate would be so responsive in a real-world setup.
Additionally, the project highlighted the importance of joint alignment and load distribution, as minor adjustments in the CAD design greatly influenced the arm's stability and fluidity. This experience deepened my understanding of mechanical and electrical integration, showcasing the potential of combining custom design, Arduino programming, and real-time control systems in robotics
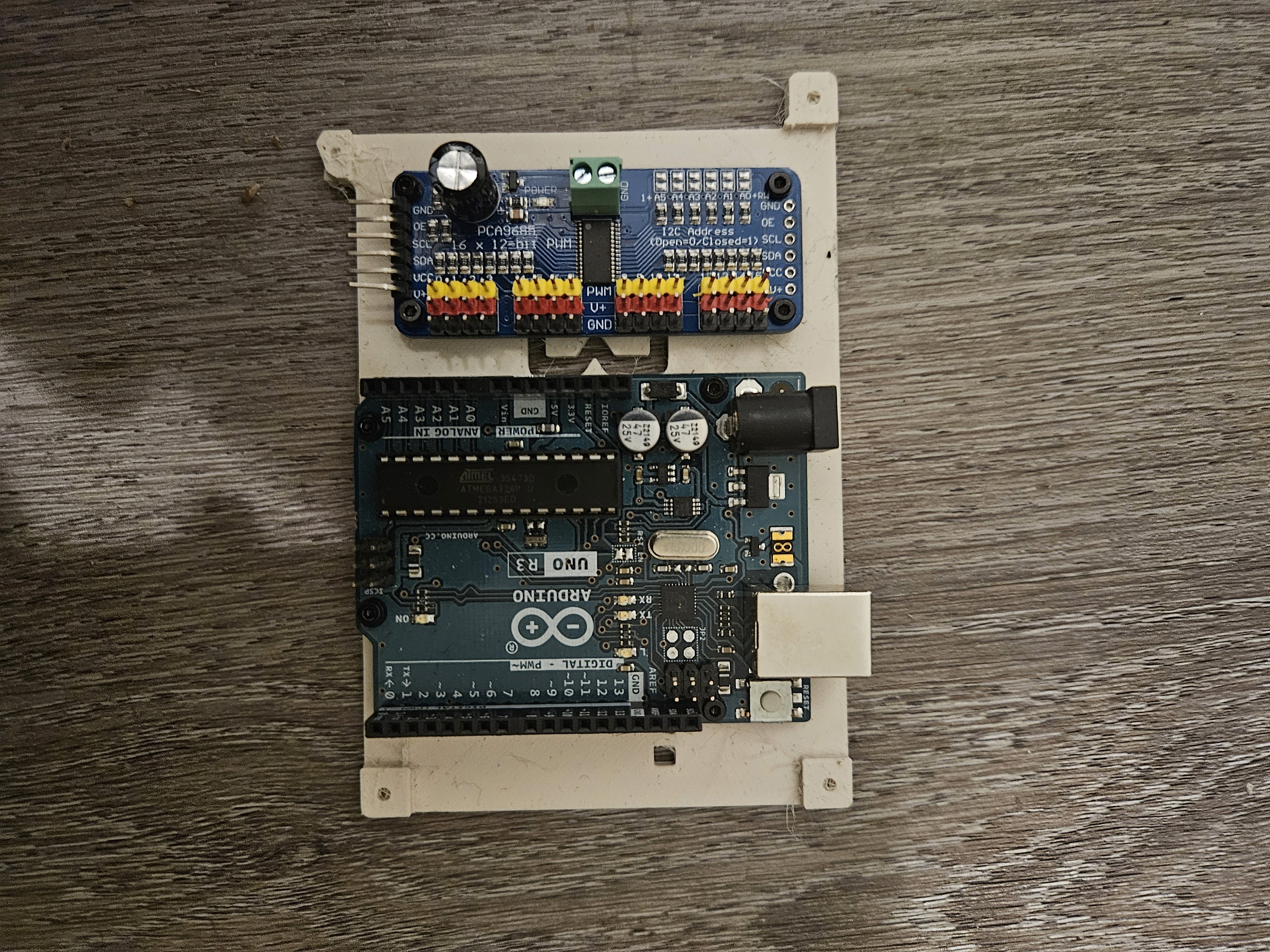
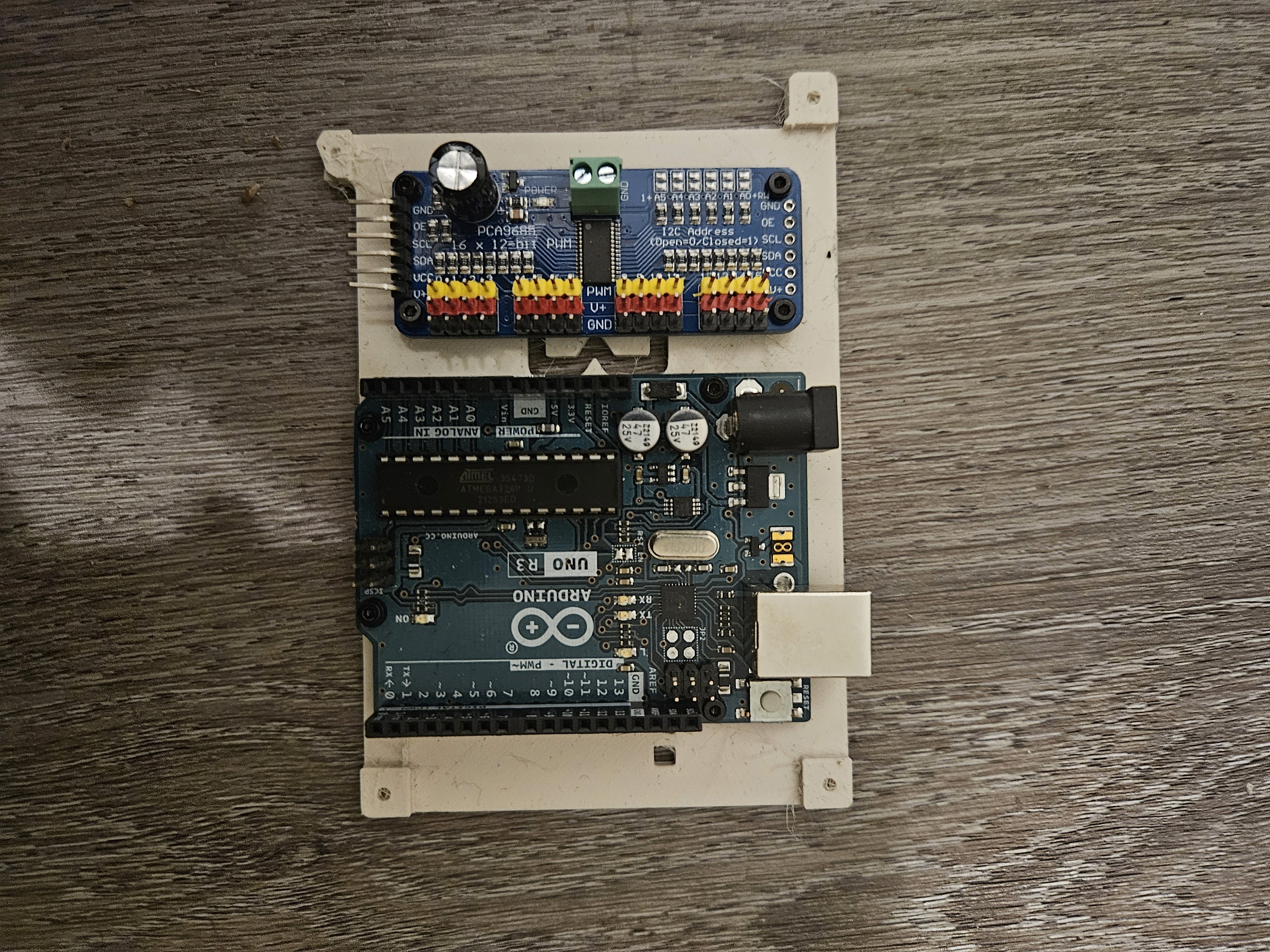


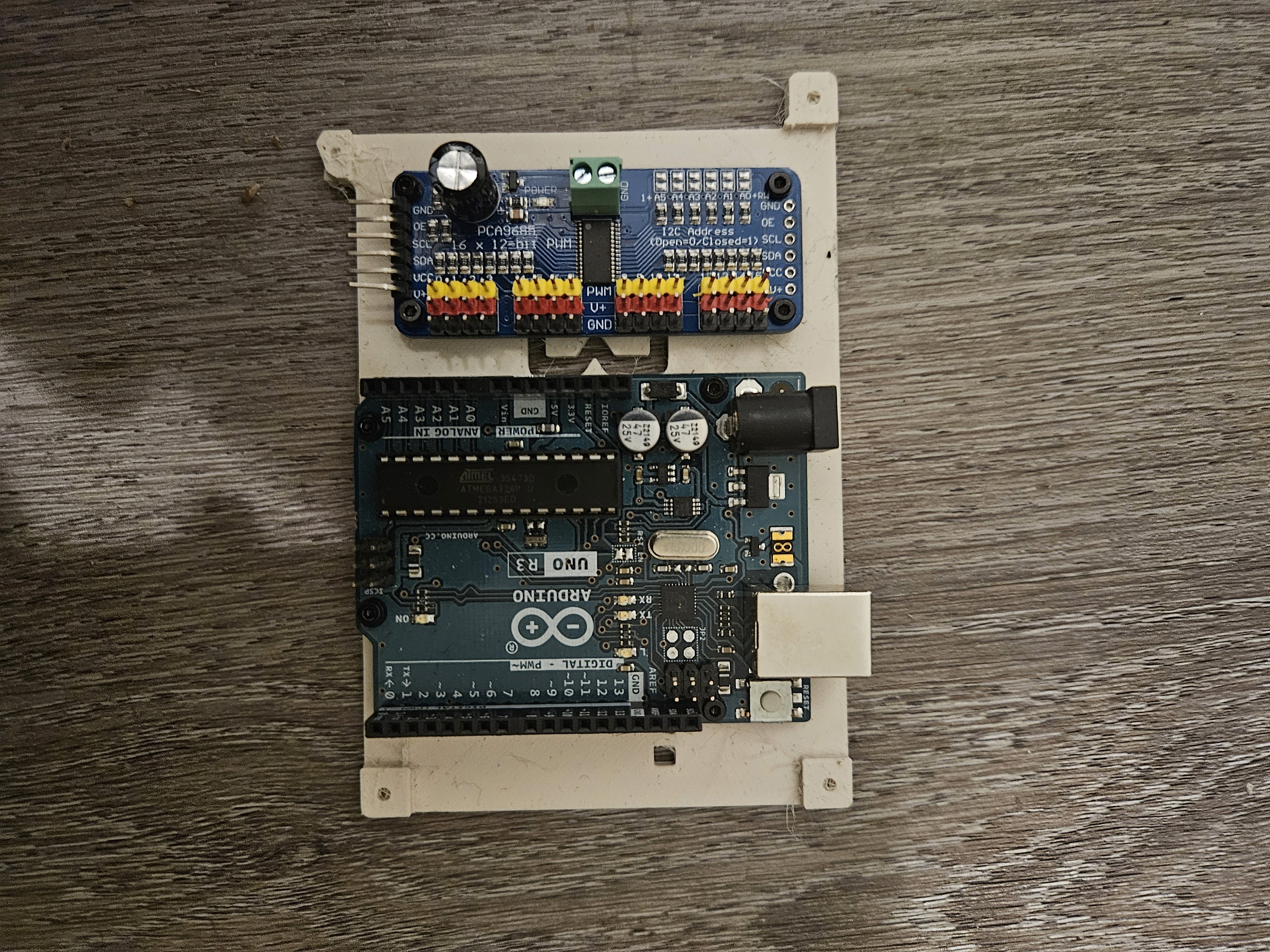
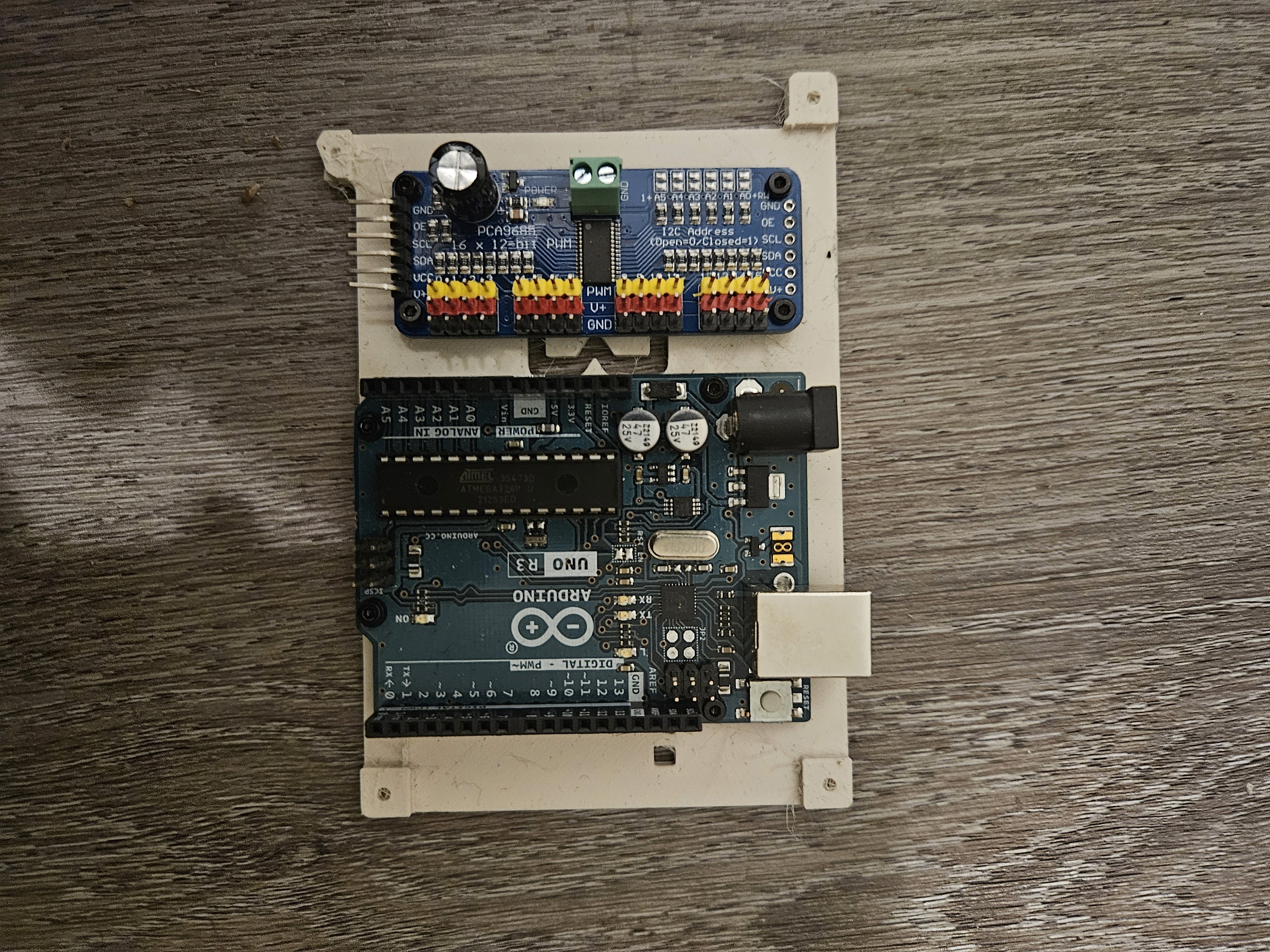


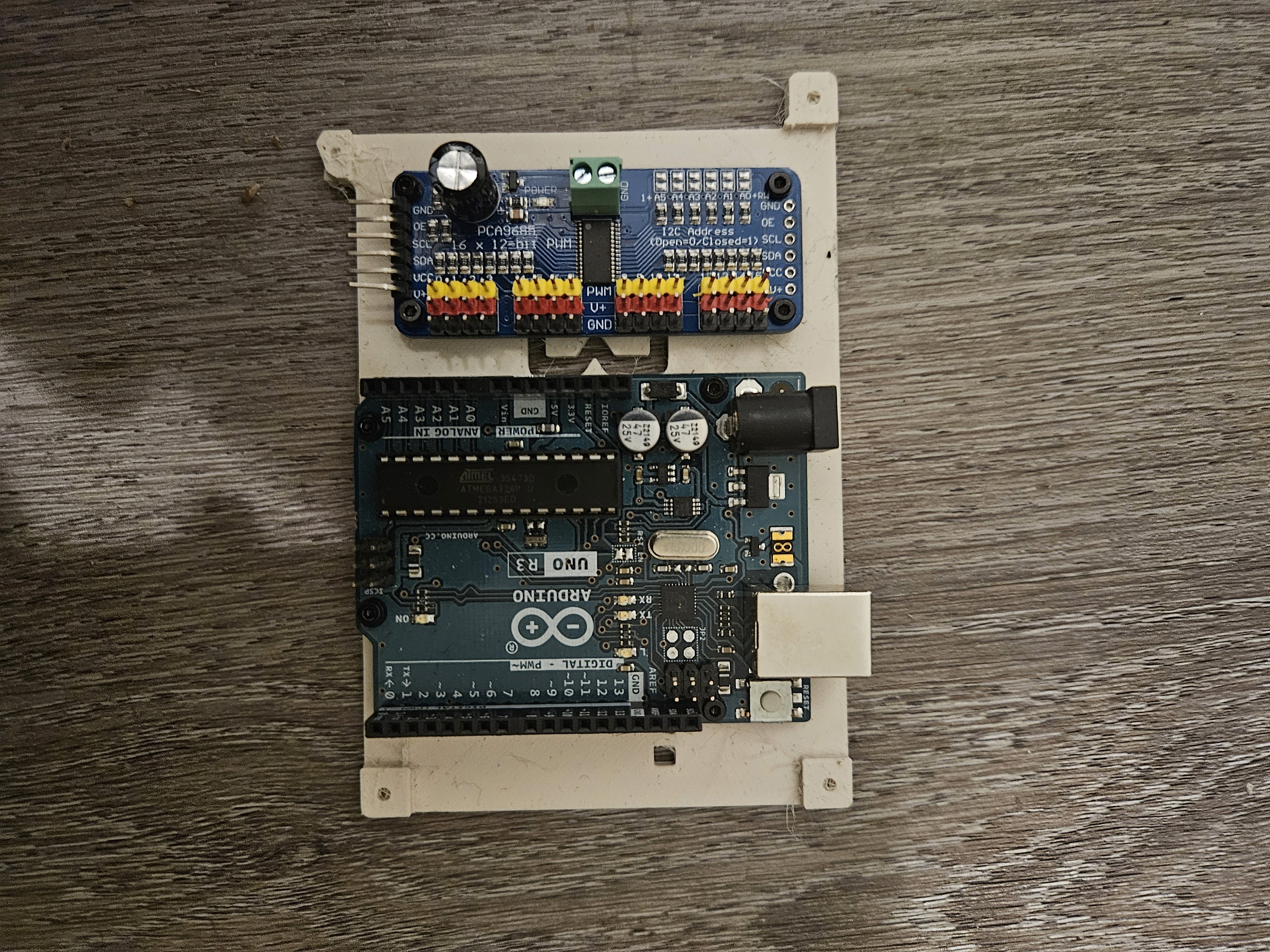

